పాలిషింగ్ యొక్క సారాంశం మరియు అమలు
మేము యాంత్రిక భాగాలపై ఉపరితల ప్రాసెసింగ్ ఎందుకు చేయాలి?
ఉపరితల చికిత్స ప్రక్రియ వేర్వేరు ప్రయోజనాల కోసం భిన్నంగా ఉంటుంది.
1 యాంత్రిక భాగాల ఉపరితల ప్రాసెసింగ్ యొక్క మూడు ప్రయోజనాలు:
1.1 పార్ట్ ఖచ్చితత్వాన్ని పొందటానికి ఉపరితల ప్రాసెసింగ్ పద్ధతి
మ్యాచింగ్ అవసరాలతో ఉన్న భాగాల కోసం, ఖచ్చితత్వం కోసం అవసరాలు (డైమెన్షనల్ ఖచ్చితత్వం, ఆకార ఖచ్చితత్వం మరియు స్థానం ఖచ్చితత్వంతో సహా) సాధారణంగా సాపేక్షంగా ఎక్కువగా ఉంటాయి మరియు ఖచ్చితత్వం మరియు ఉపరితల కరుకుదనం సంబంధించినవి. ఖచ్చితత్వం పొందడానికి, సంబంధిత కరుకుదనాన్ని సాధించాలి. ఉదాహరణకు: ఖచ్చితత్వం IT6 సాధారణంగా సంబంధిత కరుకుదనం RA0.8 అవసరం.
[సాధారణ యాంత్రిక మార్గాలు]:
- టర్నింగ్ లేదా మిల్లింగ్
- ఫైన్ బోరింగ్
- ఫైన్ గ్రౌండింగ్
- గ్రౌండింగ్
1.2 ఉపరితల యాంత్రిక లక్షణాలను పొందటానికి ఉపరితల ప్రాసెసింగ్ పద్ధతులు
1.2.1 దుస్తులు నిరోధకతను పొందడం
[[సాధారణ పద్ధతులు
- గట్టిపడటం లేదా కార్బరైజింగ్/అణచివేత తర్వాత గ్రౌండింగ్ (నైట్రిడింగ్)
- హార్డ్ క్రోమ్ లేపనం తర్వాత గ్రౌండింగ్ మరియు పాలిషింగ్
1.2.2 మంచి ఉపరితల ఒత్తిడి స్థితిని పొందడం
[[సాధారణ పద్ధతులు
- మాడ్యులేషన్ మరియు గ్రౌండింగ్
- ఉపరితల ఉష్ణ చికిత్స మరియు గ్రౌండింగ్
- ఉపరితల రోలింగ్ లేదా షాట్ పీనింగ్ తరువాత చక్కటి గ్రౌండింగ్
1.3 ఉపరితల రసాయన లక్షణాలను పొందటానికి ప్రాసెసింగ్ పద్ధతులు
[[సాధారణ పద్ధతులు
- ఎలక్ట్రోప్లేటింగ్ మరియు పాలిషింగ్
2 మెటల్ ఉపరితల పాలిషింగ్ టెక్నాలజీ
2.1 ప్రాముఖ్యత ఇది ఉపరితల సాంకేతికత మరియు ఇంజనీరింగ్ రంగంలో ఒక ముఖ్యమైన భాగం, మరియు పారిశ్రామిక ఉత్పత్తి ప్రక్రియలలో, ముఖ్యంగా ఎలక్ట్రోప్లేటింగ్ పరిశ్రమ, పూత, యానోడైజింగ్ మరియు వివిధ ఉపరితల చికిత్స ప్రక్రియలలో విస్తృతంగా ఉపయోగించబడుతుంది.
2.2 ప్రారంభ ఉపరితల పారామితులు మరియు వర్క్పీస్ యొక్క సాధించిన ప్రభావ పారామితులు ఎందుకు అంత ముఖ్యమైనవి?ఎందుకంటే అవి పాలిషింగ్ పని యొక్క ప్రారంభ మరియు లక్ష్య బిందువులు, ఇది పాలిషింగ్ మెషీన్ రకాన్ని ఎలా ఎంచుకోవాలో, అలాగే పాలిషింగ్ మెషీన్కు అవసరమైన గ్రౌండింగ్ హెడ్స్, మెటీరియల్ రకం, ఖర్చు మరియు సామర్థ్యాన్ని ఎలా ఎంచుకోవాలో నిర్ణయిస్తుంది.
2.3 గ్రౌండింగ్ & పాలిషింగ్ దశలు మరియు పథాలు
యొక్క నాలుగు సాధారణ దశలుగ్రౌండింగ్మరియుపాలిషింగ్]: వర్క్పీస్ యొక్క ప్రారంభ మరియు చివరి కరుకుదనం విలువల ప్రకారం, ముతక గ్రౌండింగ్ - చక్కటి గ్రౌండింగ్ - చక్కటి గ్రౌండింగ్ - పాలిషింగ్. రాబ్రేసివ్లు ముతక నుండి జరిమానా వరకు ఉంటాయి. గ్రౌండింగ్ సాధనం మరియు వర్క్పీస్ మార్చబడిన ప్రతిసారీ శుభ్రం చేయాలి.
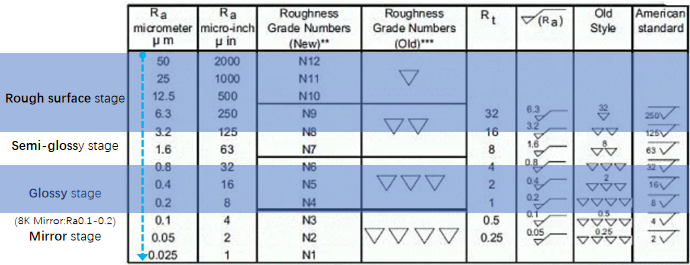
2.3.1 గ్రౌండింగ్ సాధనం కష్టం, మైక్రో కట్టింగ్ మరియు ఎక్స్ట్రాషన్ ప్రభావం ఎక్కువగా ఉంటుంది మరియు పరిమాణం మరియు కరుకుదనం స్పష్టమైన మార్పులను కలిగి ఉంటాయి.
2.3.2 మెకానికల్ పాలిషింగ్ గ్రౌండింగ్ కంటే సున్నితమైన కట్టింగ్ ప్రక్రియ. పాలిషింగ్ సాధనం మృదువైన పదార్థంతో తయారు చేయబడింది, ఇది కరుకుదనాన్ని మాత్రమే తగ్గిస్తుంది కాని పరిమాణం మరియు ఆకారం యొక్క ఖచ్చితత్వాన్ని మార్చదు. కరుకుదనం 0.4μm కన్నా తక్కువకు చేరుకుంటుంది.
2.4 ఉపరితల ముగింపు చికిత్స యొక్క మూడు ఉప-భావనలు: గ్రౌండింగ్, పాలిషింగ్ మరియు ఫినిషింగ్
2.4.1 మెకానికల్ గ్రౌండింగ్ మరియు పాలిషింగ్ యొక్క భావన
యాంత్రిక గ్రౌండింగ్ మరియు మెకానికల్ పాలిషింగ్ రెండూ ఉపరితల కరుకుదనాన్ని తగ్గించగలిగినప్పటికీ, తేడాలు కూడా ఉన్నాయి:
- 【మెకానికల్ పాలిషింగ్】: ఇందులో డైమెన్షనల్ టాలరెన్స్, షేప్ టాలరెన్స్ మరియు పొజిషన్ టాలరెన్స్ ఉన్నాయి. ఇది కరుకుదనాన్ని తగ్గించేటప్పుడు డైమెన్షనల్ టాలరెన్స్, షేప్ టాలరెన్స్ మరియు గ్రౌండ్ ఉపరితలం యొక్క స్థాన సహనాన్ని నిర్ధారించాలి.
- మెకానికల్ పాలిషింగ్: ఇది పాలిషింగ్కు భిన్నంగా ఉంటుంది. ఇది ఉపరితల ముగింపును మాత్రమే మెరుగుపరుస్తుంది, కాని సహనాన్ని విశ్వసనీయంగా హామీ ఇవ్వలేము. దీని ప్రకాశం పాలిషింగ్ కంటే ఎక్కువ మరియు ప్రకాశవంతంగా ఉంటుంది. యాంత్రిక పాలిషింగ్ యొక్క సాధారణ పద్ధతి గ్రౌండింగ్.
.
భాగం ఉపరితలం యొక్క ఖచ్చితత్వం మరియు కరుకుదనం దాని జీవితం మరియు నాణ్యతపై గొప్ప ప్రభావాన్ని చూపుతుంది. EDM వదిలిపెట్టిన క్షీణించిన పొర మరియు గ్రౌండింగ్ ద్వారా మిగిలిపోయిన మైక్రో పగుళ్లు భాగాల సేవా జీవితాన్ని ప్రభావితం చేస్తాయి.
Process ఫినిషింగ్ ప్రక్రియలో చిన్న మ్యాచింగ్ భత్యం ఉంది మరియు ప్రధానంగా ఉపరితల నాణ్యతను మెరుగుపరచడానికి దీనిని ఉపయోగిస్తారు. మ్యాచింగ్ ఖచ్చితత్వాన్ని మెరుగుపరచడానికి ఒక చిన్న మొత్తాన్ని ఉపయోగిస్తారు (డైమెన్షనల్ ఖచ్చితత్వం మరియు ఆకార ఖచ్చితత్వం వంటివి), కానీ స్థానం ఖచ్చితత్వాన్ని మెరుగుపరచడానికి ఇది ఉపయోగించబడదు.
② పూర్తి చేయడం అంటే మైక్రో కట్టింగ్ మరియు వర్క్పీస్ ఉపరితలాన్ని చక్కటి-కణిత రాపిడితో వెలికితీసే ప్రక్రియ. ఉపరితలం సమానంగా ప్రాసెస్ చేయబడుతుంది, కట్టింగ్ ఫోర్స్ మరియు కట్టింగ్ వేడి చాలా చిన్నవి, మరియు చాలా ఎక్కువ ఉపరితల నాణ్యతను పొందవచ్చు. ③ పూర్తి చేయడం అనేది సూక్ష్మ ప్రాసెసింగ్ ప్రక్రియ మరియు పెద్ద ఉపరితల లోపాలను సరిదిద్దలేవు. ప్రాసెసింగ్ ముందు చక్కటి ప్రాసెసింగ్ చేయాలి.
లోహ ఉపరితల పాలిషింగ్ యొక్క సారాంశం ఉపరితల ఎంపిక మైక్రో-రిమూవల్ ప్రాసెసింగ్.
3. ప్రస్తుతం పరిపక్వ పాలిషింగ్ ప్రాసెస్ పద్ధతులు: 3.1 మెకానికల్ పాలిషింగ్, 3.2 కెమికల్ పాలిషింగ్, 3.3 ఎలక్ట్రోలైటిక్ పాలిషింగ్, 3.4 అల్ట్రాసోనిక్ పాలిషింగ్, 3.5 ఫ్లూయిడ్ పాలిషింగ్, 3.6 మాగ్నెటిక్ గ్రౌండింగ్ పాలిషింగ్,
3.1 మెకానికల్ పాలిషింగ్
మెకానికల్ పాలిషింగ్ అనేది ఒక పాలిషింగ్ పద్ధతి, ఇది మృదువైన ఉపరితలాన్ని పొందటానికి పాలిష్ చేసిన ప్రోట్రూషన్లను తొలగించడానికి పదార్థ ఉపరితలం యొక్క కట్టింగ్ మరియు ప్లాస్టిక్ వైకల్యం మీద ఆధారపడుతుంది.
ఈ సాంకేతిక పరిజ్ఞానాన్ని ఉపయోగించి, యాంత్రిక పాలిషింగ్ RA0.008μm యొక్క ఉపరితల కరుకుదనాన్ని సాధించగలదు, ఇది వివిధ పాలిషింగ్ పద్ధతులలో అత్యధికం. ఈ పద్ధతి తరచుగా ఆప్టికల్ లెన్స్ అచ్చులలో ఉపయోగించబడుతుంది.
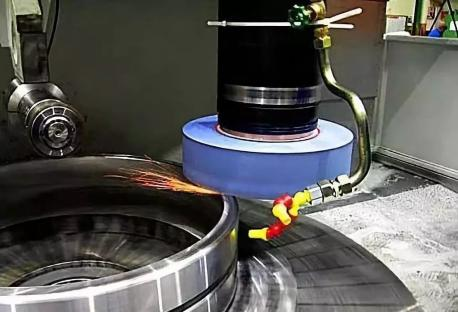
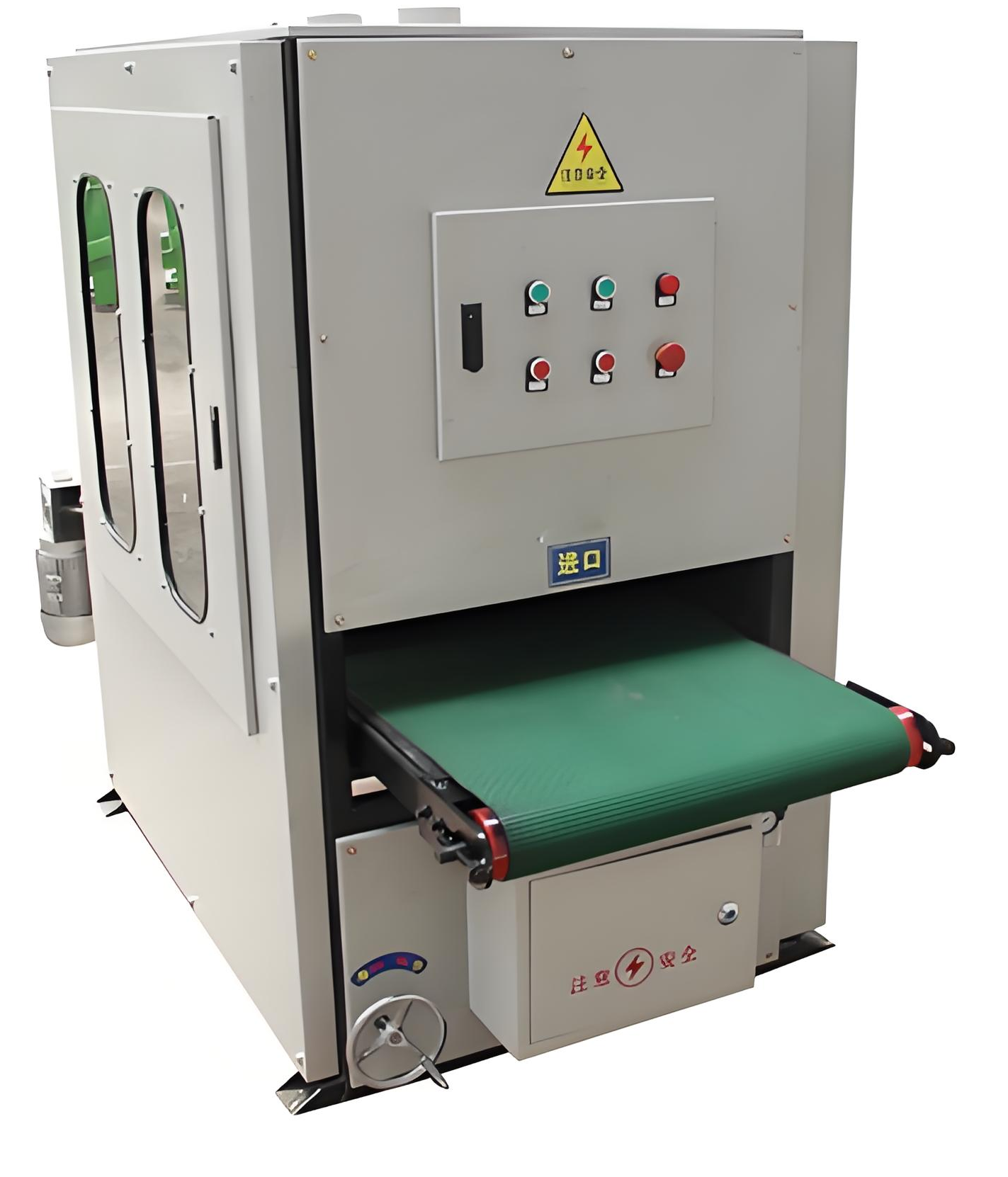
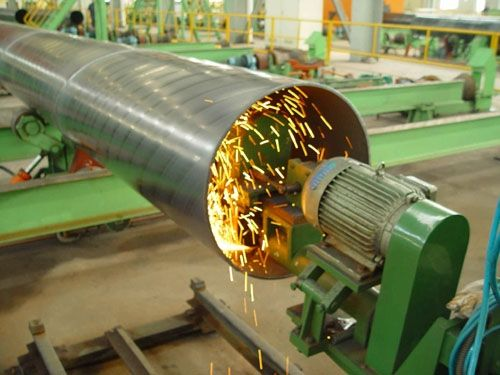
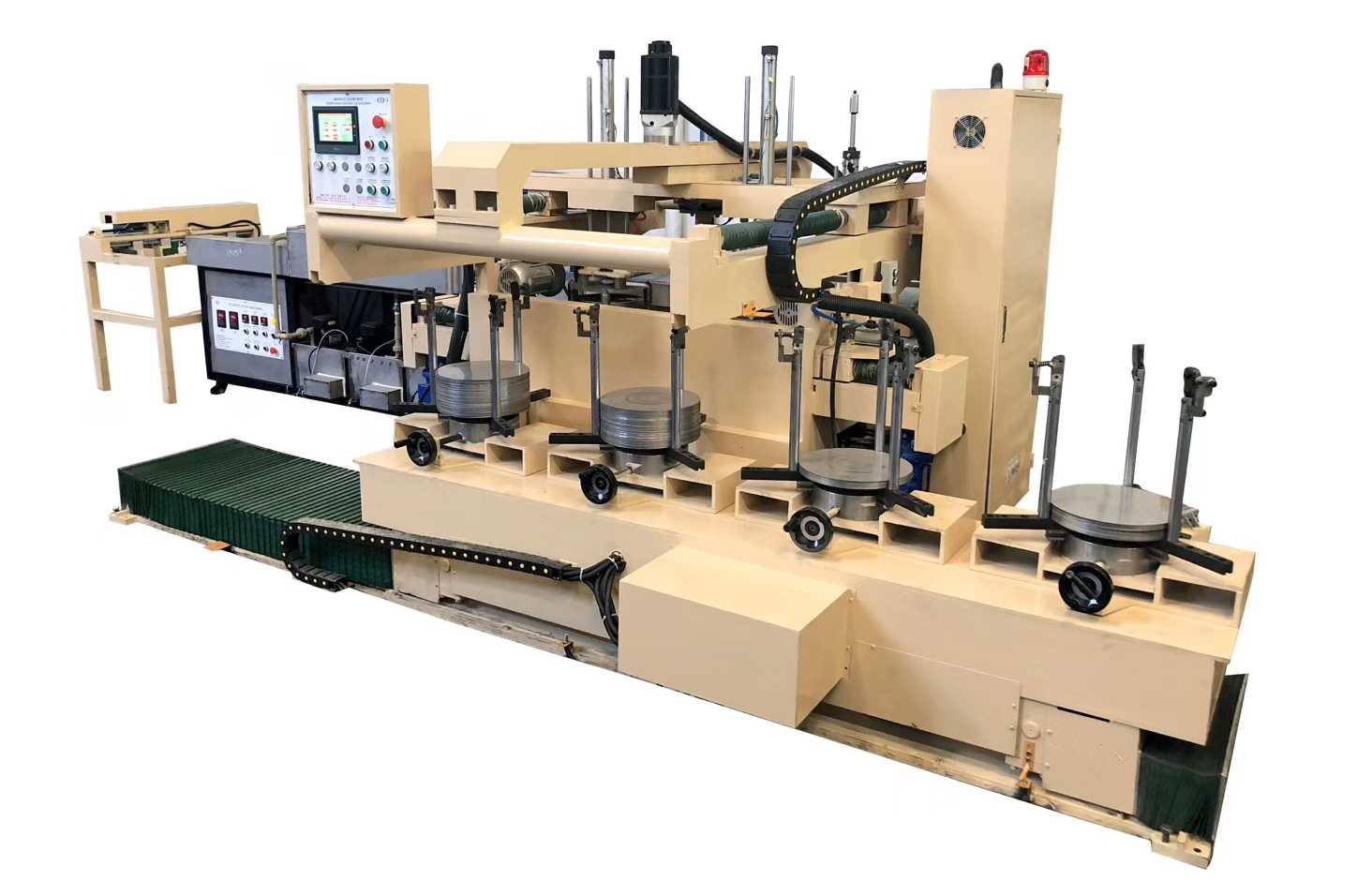
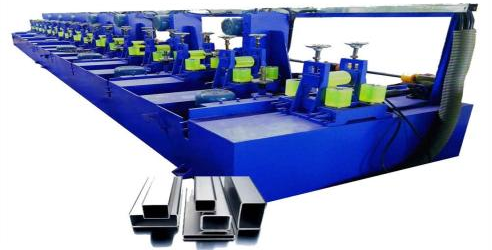
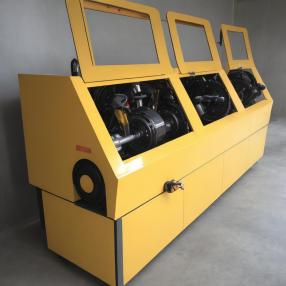
3.2 రసాయన పాలిషింగ్
రసాయన పాలిషింగ్ అంటే పదార్థ ఉపరితలం యొక్క సూక్ష్మ కుంభాకార భాగాలు రసాయన మాధ్యమంలో పుటాకార భాగాలపై ప్రాధాన్యంగా కరిగిపోతాయి, తద్వారా మృదువైన ఉపరితలం పొందవచ్చు. ఈ పద్ధతి యొక్క ప్రధాన ప్రయోజనాలు ఏమిటంటే, దీనికి సంక్లిష్టమైన పరికరాలు అవసరం లేదు, సంక్లిష్ట ఆకృతులతో వర్క్పీస్లను మెరుగుపరుస్తుంది, ఒకే సమయంలో అనేక వర్క్పీస్లను మెరుగుపరుస్తుంది మరియు చాలా సమర్థవంతంగా ఉంటుంది. రసాయన పాలిషింగ్ యొక్క ప్రధాన సమస్య పాలిషింగ్ ద్రవ తయారీ. రసాయన పాలిషింగ్ ద్వారా పొందిన ఉపరితల కరుకుదనం సాధారణంగా అనేక పదుల μm.
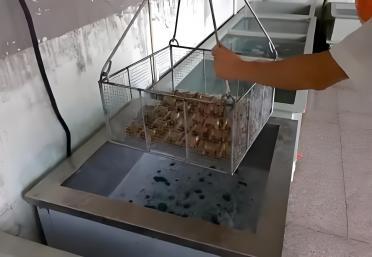
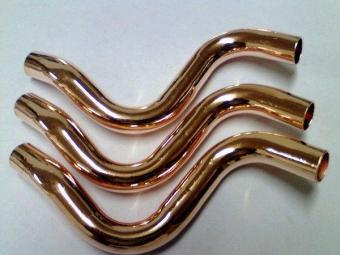

3.3 ఎలక్ట్రోలైటిక్ పాలిషింగ్
ఎలక్ట్రోలైటిక్ పాలిషింగ్, ఎలెక్ట్రోకెమికల్ పాలిషింగ్ అని కూడా పిలుస్తారు, ఉపరితలం మృదువైనదిగా చేయడానికి పదార్థం యొక్క ఉపరితలంపై చిన్న ప్రోట్రూషన్లను ఎంపిక చేస్తుంది.
రసాయన పాలిషింగ్తో పోలిస్తే, కాథోడ్ ప్రతిచర్య యొక్క ప్రభావాన్ని తొలగించవచ్చు మరియు ప్రభావం మంచిది. ఎలెక్ట్రోకెమికల్ పాలిషింగ్ ప్రక్రియ రెండు దశలుగా విభజించబడింది:
.
(2) గ్లోస్ స్మూతీంగ్: అనోడిక్ ధ్రువణత: ఉపరితల ప్రకాశం మెరుగుపరచబడింది, రాల్ μm.
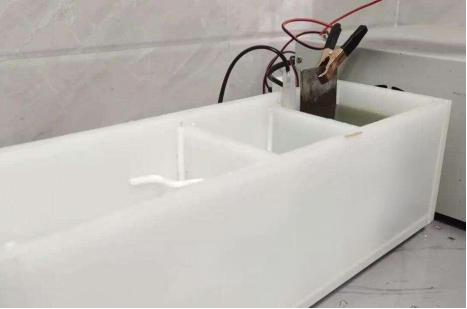
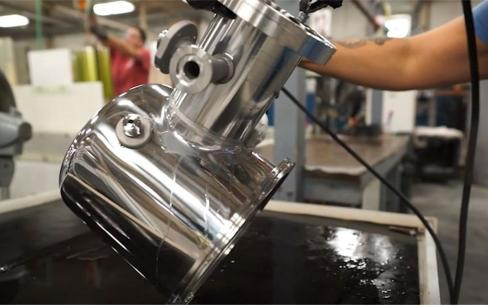
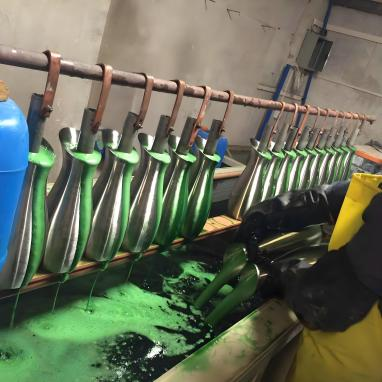
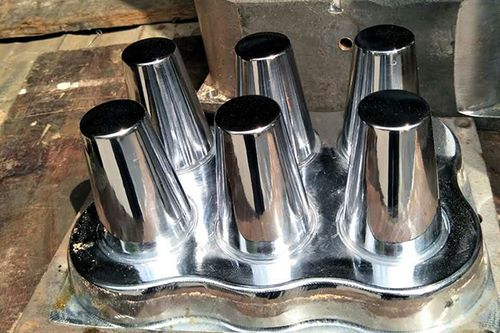
3.4 అల్ట్రాసోనిక్ పాలిషింగ్
వర్క్పీస్ను రాపిడి సస్పెన్షన్లో ఉంచి అల్ట్రాసోనిక్ ఫీల్డ్లో ఉంచారు. రాపిడి భూమి మరియు అల్ట్రాసోనిక్ వేవ్ యొక్క డోలనం ద్వారా వర్క్పీస్ ఉపరితలంపై పాలిష్ చేయబడింది. అల్ట్రాసోనిక్ మ్యాచింగ్ ఒక చిన్న మాక్రోస్కోపిక్ శక్తిని కలిగి ఉంది మరియు వర్క్పీస్ యొక్క వైకల్యానికి కారణం కాదు, కానీ సాధనం తయారు చేయడం మరియు వ్యవస్థాపించడం కష్టం.
అల్ట్రాసోనిక్ మ్యాచింగ్ను రసాయన లేదా ఎలక్ట్రోకెమికల్ పద్ధతులతో కలపవచ్చు. పరిష్కారం తుప్పు మరియు విద్యుద్విశ్లేషణ ఆధారంగా, వర్క్పీస్ ఉపరితలంపై కరిగిన ఉత్పత్తులను వేరు చేయడానికి మరియు ఉపరితల యూనిఫాం దగ్గర తుప్పు లేదా ఎలక్ట్రోలైట్ చేయడానికి ద్రావణాన్ని కదిలించడానికి అల్ట్రాసోనిక్ వైబ్రేషన్ వర్తించబడుతుంది; ద్రవంలో అల్ట్రాసోనిక్ తరంగాల యొక్క పుచ్చు ప్రభావం తుప్పు ప్రక్రియను కూడా నిరోధిస్తుంది మరియు ఉపరితల ప్రకాశాన్ని సులభతరం చేస్తుంది.
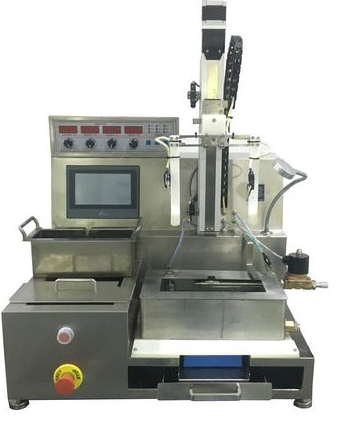
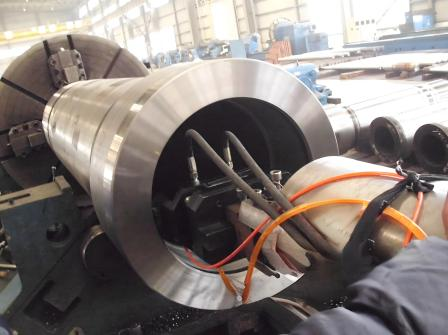
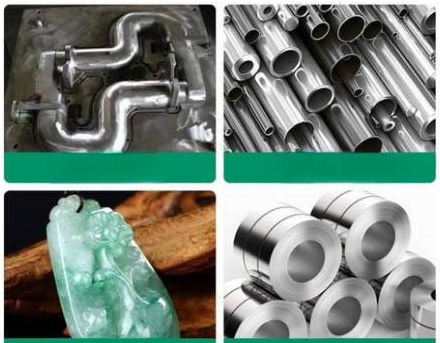
3.5 ద్రవ పాలిషింగ్
ద్రవ పాలిషింగ్ హై-స్పీడ్ ప్రవహించే ద్రవం మరియు పాలిషింగ్ యొక్క ఉద్దేశ్యాన్ని సాధించడానికి వర్క్పీస్ ఉపరితలాన్ని బ్రష్ చేయడానికి తీసుకువెళ్ళే రాపిడి కణాలపై ఆధారపడుతుంది.
సాధారణంగా ఉపయోగించే పద్ధతులు: రాపిడి జెట్ ప్రాసెసింగ్, లిక్విడ్ జెట్ ప్రాసెసింగ్, ఫ్లూయిడ్ డైనమిక్ గ్రౌండింగ్ మొదలైనవి.

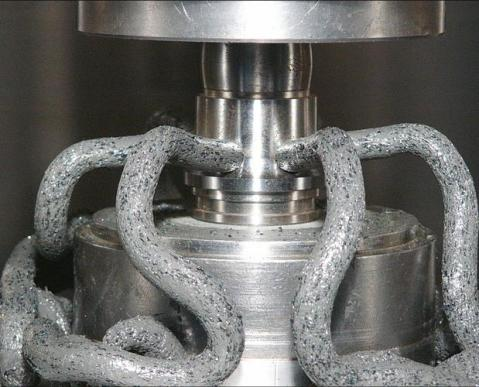
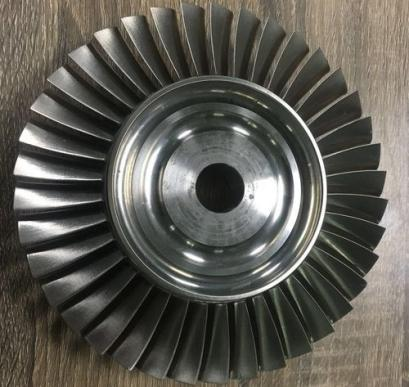
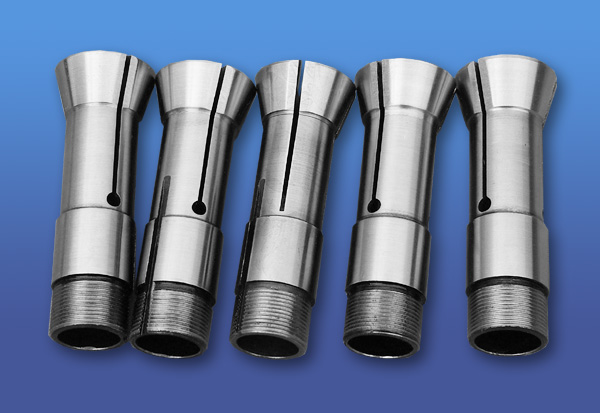
3.6 మాగ్నెటిక్ గ్రౌండింగ్ మరియు పాలిషింగ్
మాగ్నెటిక్ గ్రౌండింగ్ మరియు పాలిషింగ్ వర్క్పీస్ను రుబ్బుకోవడానికి అయస్కాంత క్షేత్రం యొక్క చర్య కింద రాపిడి బ్రష్లను ఏర్పరుస్తుంది.
ఈ పద్ధతిలో అధిక ప్రాసెసింగ్ సామర్థ్యం, మంచి నాణ్యత, ప్రాసెసింగ్ పరిస్థితులపై సులభమైన నియంత్రణ మరియు మంచి పని పరిస్థితులు ఉన్నాయి. తగిన రాపిడితో, ఉపరితల కరుకుదనం RA0.1μm కు చేరుకుంటుంది.
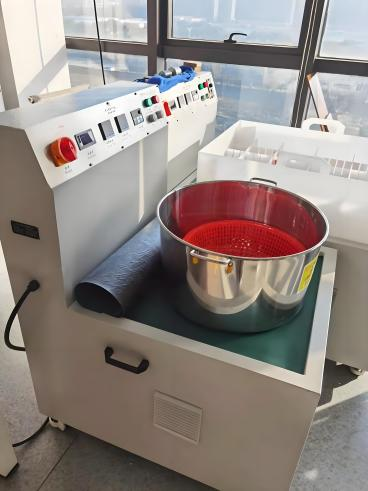
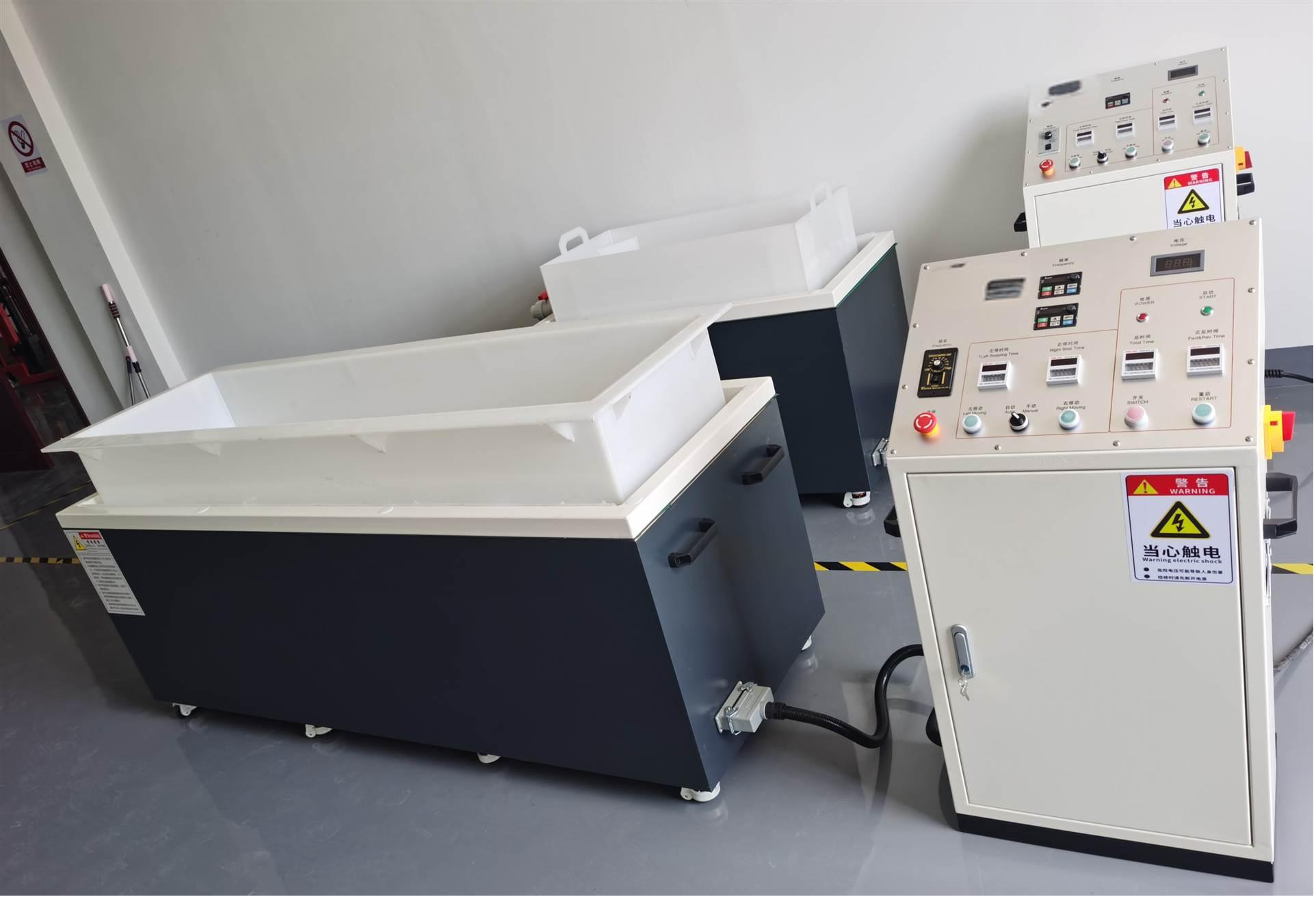
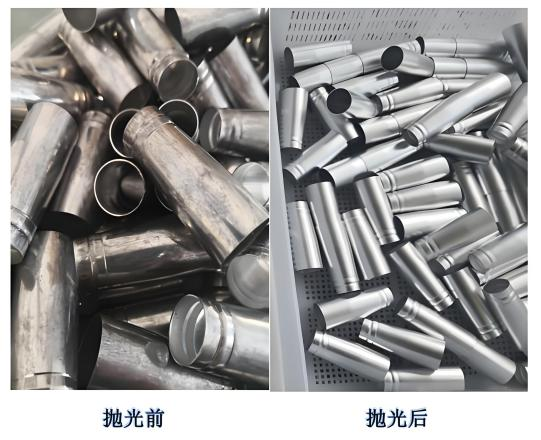
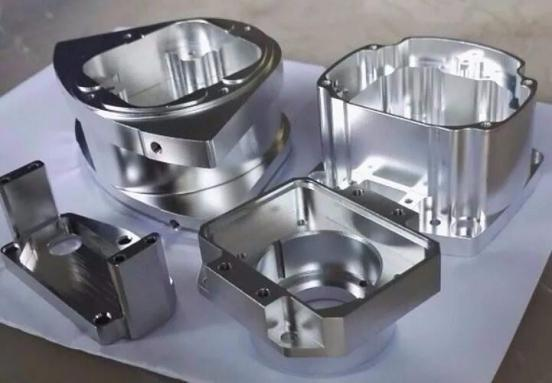
ఈ వ్యాసం ద్వారా, మీరు పాలిషింగ్ గురించి మంచి అవగాహన కలిగి ఉంటారని నేను నమ్ముతున్నాను. వివిధ రకాల పాలిషింగ్ యంత్రాలు వేర్వేరు వర్క్పీస్ పాలిషింగ్ లక్ష్యాలను సాధించే ప్రభావం, సామర్థ్యం, ఖర్చు మరియు ఇతర సూచికలను నిర్ణయిస్తాయి.
మీ కంపెనీ లేదా మీ కస్టమర్లకు అవసరమైన పాలిషింగ్ మెషీన్ వర్క్పీస్ ప్రకారం మాత్రమే సరిపోలాలి, కానీ యూజర్ యొక్క మార్కెట్ డిమాండ్, ఆర్థిక పరిస్థితి, వ్యాపార అభివృద్ధి మరియు ఇతర అంశాల ఆధారంగా కూడా సరిపోతుంది.
వాస్తవానికి, దీనిని ఎదుర్కోవటానికి సరళమైన మరియు సమర్థవంతమైన మార్గం ఉంది. మీకు సహాయం చేయడానికి దయచేసి మా ప్రీ-సేల్స్ సిబ్బందిని సంప్రదించండి.
పోస్ట్ సమయం: జూన్ -17-2024